Most of the monitors I use (including this one) are repaired units that
people have discarded or recycled. If you have just a little bit
of tech know-how and a decent parts bin, you can usually get these
discarded monitors running again. This saves space at the
landfill and cuts down on the hazardous waste generation. Plus,
you can donate any extra monitors you have to friends, churches, clubs,
or charities that can use a hand.
And consider taking some fixed monitors down to the city government
offices, to discourage them from running reclaiming drives and instead
running reuse/repurpose drives!
I recently donated four of my repaired monitors to the local Seniors
Center. Lots of people on fixed incomes may have been given a
system or had one for several years, but can't afford to replace a
monitor that goes out. My afternoon's entertainment fixing a
monitor may help someone out of a tight spot
The external power supply
In a surprising number of cases, nothing is wrong with the monitor
itself. Those monitors that use a lump-in-the-line or brick power
supply usually had a bad supply. If you get an LCD that has a
small power jack in the back (like the coaxial power connectors common
on most devices), try finding a suitable replacement power
supply. You will need to check the ratings for the monitor on the
back panel to get the voltage and current required. This is
usually something like 12 VDC at 2.0 Amps or so. Go to a surplus
shop, root through the junk power supply bin, and find a supply that
matches these ratings. Note that going to a larger number on the
current (Amps) is OK, but you have to match the voltage exactly!
Note that you must also find a matching power connector! Take the
monitor with you when you look for a power supply. When you find
a suitable supply, check that the connector on the supply mates
properly with the jack on the back of the monitor WITHOUT APPLYING
POWER! If the two connectors don't mate, find a second supply
with a connector that does mate, even if the voltage or current are
wrong. You will later cut the connector off this second supply
and splice it onto the cord of the first supply.
When you get home, you have one last item to check before powering up
your new monitor. The center pin of the monitor's power jack
could be either negative or positive. Whichever it is, your
replacement power supply must be wired the same way. If you're
lucky, the back of the monitor will give you that
information. If it doesn't, use a voltmeter to check the
resistance between the center pin and some metal point on the monitor's
frame. If you get less than 5 ohms, the jack is wired
center-negative (the less common). If you get more than 5 ohms,
you should wire your power supply as center-positive.
Compare the polarity your monitor expects to the polarity of the power
supply you chose (the one that provides the proper voltage and
current). If the power supply plug is the right polarity, it
fits, and the voltage/current are correct, you are ready to go; move to
the next step where you try out the supply. If the polarity is
not correct, you need to cut the power supply output cord (the one with
the plug on it) about six inches from the power plug, then rewire the
plug with the two wires swapped; be sure to solder your connections and
use heatshrink or tape over the splices. If you also need to
change the plug by using the second power supply you chose, cut the
output wire on the second supply about six inches from the end of its
plug and splice the plug onto the output cable of the first supply; be
sure to get the polarity right and to solder your connections and use
heatshrink or tape over the splices.
Now that your power supply is ready to go, plug it into the monitor,
hook the monitor to a PC, plug the power supply into the wall, and boot
the PC. If the power supply was the problem, you should see the
monitor light up. You're done!
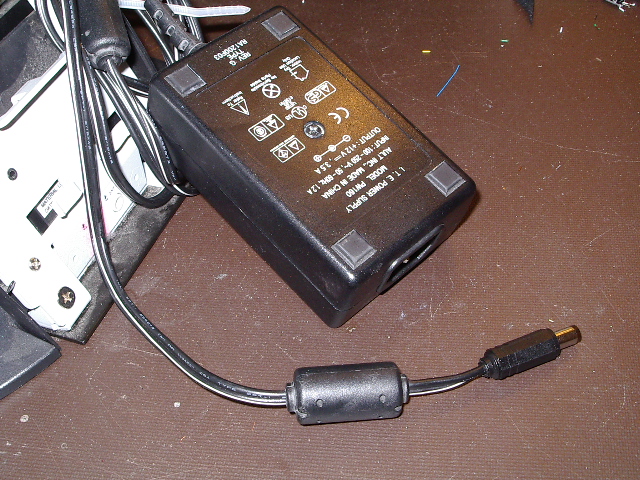
Here I've replaced the plug on an old lump-in-the-line power supply to
match a discarded ViewSonic VX500 (a really nice monitor, BTW).
The photo shows the voltage and current rating of the supply. I
had to solder the two wires from the power supply to match the polarity
required by the VX500; it wants center-positive.
120 VAC monitors (and some that use
external supplies!)
Often, defective monitors have issues on the main power board.
Such monitors can show a wide variety of failures, such as not powering
up, flashing the display on and off, or working for a while, then going
dark. The first step is to unplug the AC cord, open the back of
the
monitor, and inspect the power supply board (the board with the
largest, heavy-duty components on it). Look for any electrolytic
capacitors that are damaged or disfigured in any way. Sometimes
you'll see one that has burst its top or that has a bulging top.
The top of each electrolytic cap should be flat and shiny. Also
look for damage on the bottom of each electrolytic; sometimes these
caps will rupture where the leads come out.
If you find a damaged cap, you have to replace it with a similar
unit. Note the capacitance and voltage of the bad cap; this will
usually be something like 10 uF at 25 VDC. You must use a
replacement that has at least the same working voltage and at least the
same capacitance. You can go as much above the original voltage
as you want, but don't go any more than twice the original capacitance.
IMPORTANT! The replacement capacitor MUST be rated at 105
decC! Do not try to use a cheaper 85 degC capacitor! You
can find 105 degC caps at Fry's, Digikey, Mouser, or most TV repair
shops or suppliers.
Remove the defective cap, taking care to note the polarity.
Electrolytic caps have positive and negative leads and have to be
soldered into the circuit with these leads in the proper location; put
the replacement cap in the board in the same polarity as the
original. Solder the leads in place, then clip them off on the
underside of the board so you don't short-circuit something later when
you put the monitor back together.
Double-check that there are no more bad caps (you can have two or more
bad caps in one monitor). After you have replaced all the bad
caps, put the back of the monitor back on, hook up the monitor, and
apply power. In most cases, this will fix the monitor.
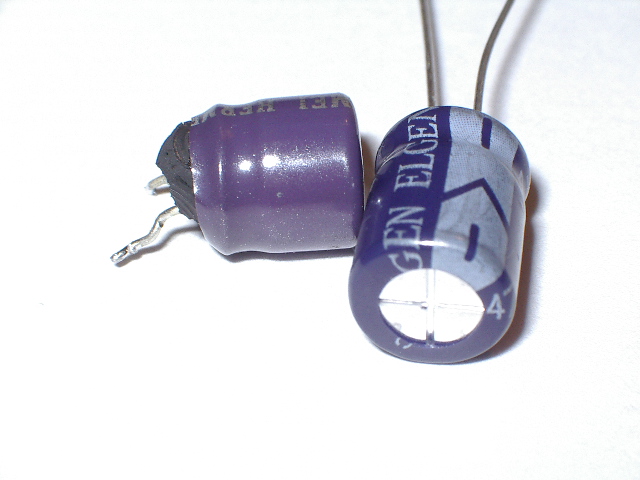
Here you see a bad capacitor on the left and a new capacitor on the
right. You can clearly see how the bad cap has burst at the
bottom near the leads. All caps in the monitor's power supply
should have smooth, flat tops like you see on the new cap. If the
top is bulging or burst, replace the cap!
Sometimes, a cap will go bad without bursting or showing any physical
damage. One monitor I worked on would run fine for a few seconds,
then go dark. It would also smell hot long before it had run long
enough to get hot under normal circumstances. After it shut down
like this once, I hurriedly reopend the back of the monitor and found a
pair of electrolytic caps that were far hotter than anything around
them, after only a few seconds of operation. I am waiting for
replacement parts, but I strongly suspect these caps were causing the
problem.
Note that most power supply boards usually have a very large
electrolytic cap somewhere near the 120 VAC connector. I have
never seen one of these go bad and comments from repair sites, notably badcaps.net, indicate that this cap
almost never fails. Doesn't mean it won't happen, but it seems
very unlikely.
Bad
solder joints
I am seeing more and more monitors with bad solder joints. I
suspect that this is an issue with the move to lead-free solder that
was started a few years ago. In years past, the solder joints on
five-year old equipment were still bright and shiny. Today,
equipment only five years old has grainy, dull, or open solder
joints. Typically, ALL of the solder joints on a power supply
board are in this condition.
I fixed one monitor where the only problem was a defective solder joint
on the main power connector. An easy fix, but it should never
have happened.
Part of my routine now is to replace whatever components are obviously
defective, then visually inspect (under magnification) all solder
joints. I have found the most problems around large-lead parts,
such as inductors or through-hole connectors; for some reason, these
connections don't age well. To repair such connections, heat the
solder joint and suck all of the old lead-free solder from the
pad. Then resolder with old-fashioned rosin-core lead solder.
Removing adhesive residue
Sometimes, a store or company will plaster an adhesive label across the
screen of a monitor they intend to dump. This always irritates
me; just because they can't/won't fix it, why do they have to make it
that much harder for someone else to work on the unit?
Regardless, you can clean up the monitor screen easily. First,
carefully peel away all of the paper label that you can. DO NOT
use a knife or other sharp instrument! Just carefully scrape the
paper away with your fingernail. Don't try to scrape off the
adhesive, you'll just mar or damage the screen.
When you have as much of the paper removed as you can, set the monitor
flat on a table with the screen facing up. Carefully pour just
enough olive oil or other light vegetable oil on the screen to cover
the adhesive. You want a small pool of oil completely covering
the adhesive. Make sure none of the oil drips into the seams of
the frame or you'll have to disassemble the unit to clean out the
oil. Leave the oil sitting on the surface of the monitor for at
least an hour.
Mop
up
the
oil
with
a soft paper towel. Then wipe the screen with a
soft paper towel that has been dampened with water and a small amount
of liquid hand soap. Follow this by wiping the screen with a
dampened paper towel (water only). Finally, clean the screen with
Windex and a soft paper towel.
If there is still adhesive left on the screen, just repeat the oiling
and cleaning treatment.
Nothing wrong!
One recent monitor, a CTL 170Lx 17-inch unit, actually didn't have
anything wrong with it at all! When I applied power, the screen
stayed dark but the little LED on the frame would blink green, then
yellow, then green, over and over. I did some web searches and
discovered that this monitor sometimes gets confused after a
power-surge or power failure. To recover, I had to reset the
monitor by holding down front-panel buttons two and three (counting
from the left) while powering up the unit, then wait until the LED
stopped blinking. Once I did that, the monitor worked
perfectly! You don't often get LCDs that are this simple to
repair, but it never hurts to check the web; it could save you the
hassle of opening up a perfectly working monitor.
(Props to Chris McLellen of Boise
LCD for this reset tip. Chris has a nice website and looks
like he offers a good service. I haven't done business with him,
but I like the attitude he shows and the fact he was willing to blog
this very helpful tip for all to use. Thanks, Chris!)
Worst case
The above paragraphs describe the problems with maybe 75% of the
monitors I've fixed. But sometimes you get a monitor that doesn't
work after trying these suggestions. At this point, you may need
to find someone with more troubleshooting skills and tools than you
have. Check the local vocational college, repair shops, or
high-tech clubs and see what you can do. At the worst, you will
end up discarding this monitor, which is how you got it in the first
place.
If you do choose to discard, PLEASE try to find a good home for the
monitor! See if there is a local Freecycle or high-tech
collection point that will hopefully get your monitor into the hands of
someone who CAN fix it and CAN reuse/repurpose it.
Monitors I've rescued...
Here are some examples of monitors I've repaired,
complete with the stories behind them.
Planar PE1700 (added 1 Nov 2010)
I found this monitor at RE-PC in Tukwilla several months
ago. This 17" monitor has a coax power connector on the back
panel, so I started out by making a new wall-wart power supply with
matching cable. However, when I plugged in the cable, the monitor
still didn't work, so I had to open the back and take a look. I
did not see any damaged or burned components, so I hooked up the power
supply and started tracing voltages. Oddly, there was no voltage
present on the PCB, even though the wall-wart power supply was
working. Turned out the coax power jack was defective. I
replaced it with one from my junk box and the monitor lit right
up. Until I got the Dell 1905FP (below), this has been my best
and favorite monitor. I think I paid $7 for it...
Dell 1905FP (added 1 Nov 2010)
I picked up this 19" monitor
at RE-PC in Tukwilla for $10. This monitor has a 120 VAC
connector on the back, so I figured I'd find bad caps in the power
supply. When I opened up the unit, I noticed three capacitors on
the power supply board were distorted. All three caps were 1000
uf at 10VDC. I didn't have any of these in my parts bin, so I
motored down to Vetco in Redmond and picked up those caps plus a good
assortment of other values to keep my junk box stocked. Vetco's
prices are a bit high, but the quality is the best. You gotta
love being able to walk into a parts store and load up on Nichicon 105
degC electrolytics on a Sunday afternoon!
I replaced the caps, put the unit back together, and fired it up; works
like a champ. This model is no longer stocked by Dell, but a
search on the Internet shows it goes for about $250 new. Highest
normal setting is 1280x1024 resolution at 75 Hz refresh, which is
certainly useable. The colors are rich and the stand it came with
has smooth, sure motion. Not bad for $15 (monitor plus caps).
LG L1933TR
(added 11 Mar 2011)
I bought this non-working 19" monitor at PC Recycle in Bellevue for
$10. It uses a 120 VAC power cord, but plugging it in yielded
nothing, not even a lit power LED. I opened the case and
immediately noticed that all of the solder joints had a grey, grainy
look to them. In the days of leaded solder, I would have called
all of them bad solder joints. Now that we're using lead-free
solder, I guess this is as good as it gets.
I replaced three caps in the power supply board; one was obviously bad,
and I replaced the other two just because. When I applied power,
the unit still didn't turn on.
Next up was resoldering the AC power connector on the main board.
I didn't see anything obviously wrong, but I have had such connections
go bad before. When I resoldered the pins, I made sure to use
leaded solder. When I applied power, still no joy.
I checked voltages at the computer board and everything looked
good. It seemed logical then that the signals from the computer
board weren't making it to the graphics connection on the LCD
panel. I reseated the small multi-pin connector at the LCD
panel. I also reheated all of the pins for that connector on the
underside of the computer board. When I applied power, I had a
beautiful LCD display.
Unforutantely, I can't say definitely that the fault lay with the
solder joints on the underside of the computer board. I suspect
that was the culprit, but I can't prove it. Oh well. $16
and a couple of entertaining hours, and I have a new monitor.
Great way to spend an afternoon.
AOC LM729 (added 20 Mar
2011)
Another $10 purchase
from PC Recycle. This monitor uses a 120 VAC power cord; when
first powered up, it showed the AOC logo and a Windows display for
about ten seconds, then the screen went dark. I opened up the
power supply and did not find any suspicious-looking caps, but I
replaced the three highest-value electrolytics on the PCB anyway, in
the "it can't hurt" philosophy. Unfortunately, it also didn't fix
the problem. It wasn't that the screen stopped receiving graphics
signals from the processor board; the drive voltage to the backlights
was cutting out.
Research on the web turned up a reference to inductors on the power
supply board of this model occasionally showing bad solder
joints. A quick look showed everything seemed fine.
However, a closer inspection under magnification showed that the solder
joints for both L201 and L202 appeared to have aged badly; one of them
was clearly open. I sucked the solder from each connection and
resoldered it; problem fixed.
This monitor has an excellent picture with good color, supports
1280x1024. It also rotates 90 degrees on its stand, but I don't
have drivers to support that feature yet.
AOC LM729 (added 20 Mar
2011)
This
is
a
second
LM729
monitor
I picked up at the same time as above, also
for $10. It showed the same problems as the first one, so I was
filled with confidence as I opened it up. Again, all of the caps
looked perfect. This time, I went straight for the two inductors
on the power supply board. As before, the solder joints for both
had a grainy appearance and while I've seen worse, I resoldered them
anyway. I also touched up several other connections, notably
those on a pair of power transistors nearby. Plugged the monitor
into a test PC I keep handy; monitor worked like a charm.
I find it odd that so many monitor makers can't get the caps right, but
AOC did. However, AOC had problems with solder joints aging on
the inductors where other makers don't. Regardless, to the
consumer the issue looks the same; the monitor stops working. Oh
well...
Viewsonic VA902b (added 27 Mar 2011)
I was in the Arlington PC Recycle and picked up this unit
for $19. This is a no-frills 19" monitor; no speakers, no DVI
connector, no USB. When I plugged it in and fed it a graphics
signal, the monitor would work fine for a second or two, go dark for a
couple of seconds, then repeat the cycle continuously. When I
opened it up, I found and replaced two bulging caps (1000uf/25V and
220uf/25V). I also replaced a second 220uf/25V cap in the same
area, just because. I double-checked the solder joints on the
underside of the power supply board and resoldered several that looked
grainy. Reassembled the monitor, plugged it in, looks
great! Total cost: about $23.
Dell 2005FPW (added 10 Apr 2011)
This was a $20 purchase from the Arlington PC
REcycle. This is a nice, 20" wide-screen monitor, no speakers,
with DVI and USB connectors. When I powered this one up, it
showed an excellent graphics picture for about three minutes, then the
screen went black. After a few seconds, the graphics image came
back on, but again when out after a few seconds. I replaced ALL
of the electrolytics on the power boards EXCEPT the largest cap near
the AC connector. The symptoms improved slightly, in that it took
longer before the screen first went black, but the problem persisted.
Research on the web shows that two caps on the logic board (C637 and
C635) are often at fault, so I replaced them; problem remained. I
replaced a couple other caps in the same area on the logic board, but
the problem was still there.
I soldered a wire to the GND connection and a wire to the 12 VDC
connection (pin 1) on the power supply board, partially reassembled the
display, then powered up the display with a meter on the wires so I
could monitor the value of the 12 VDC supply to the logic board.
The 12 VDC supply started out at about 6.35 VDC. This voltage
slowly dropped until it hit about 6.01 VDC, at which point the monitor
went dark. The supply voltage immediately started climbing until
it hit about 6.14 VDC. At this point, the display came back on,
the supply voltage dropped back to 6.01 VDC, and the display went dark
again. This cycle repeated until I shut off power.
I unsoldered the 12 VDC regulator (a KIA278R12) from the power board
and removed it from its heatsink. On my bench, applying 12.5 VDC
to the input gave me 7.5 VDC output with no load, so the regulator is
shot. I was able to find a suitable replacement from Mouser (the
Fairchild KA378R12C) and have some on order. The Fairchild part
is a 3A regulator and should prove more robust than the 2A part it is
replacing.
More on this fix later...
OK, I received the KA378R12C regulators. The first thing I did
was hook one up on my bench and check the output. As expected, it
outputs 12 VDC. I spread a little heatsink compound on the
device's back, bolted the regulator to the original heatsink, and put
the monitor back together. Works like a champ (I'm using it to
write this update).
This monitor was a bear to take apart and put back together. I
ended up loosening the adhesive tape that holds the flat ribbon cable
connecting the front-panel switch board, to give myself a little bit of
extra slack for putting the front panel back together. Even so,
this is an awkward monitor to work on. Hopefully, I've dealt with
all the issues and won't have to reopen it for a long time.
Dell E198FPb (added 11 Apr 2011)
I picked up this 19" plain-Jane (Dsub-15 VGA only)
monitor from the IT department of a local business. It was out of
warranty and had been stuck on a shelf, waiting for the recycler.
I didn't even bother to power it up so I don't know why it was labeled
BAD with a big sticker on the screen. The power supply board had
three bad caps, a pair of 680uf/16VDC and a 330uf/35VDC. I
replaced them with suitable units from my parts bin, put the monitor
back together, and it powered up just fine. This unit has a very
nice image with good color; it will make a great utility display.
Another one saved from the recycler!
Dell 1908FPt (added 1 May 2011)
Another orphan rescued from a local business, this 19" monitor is
loaded with VGA, DVI and USB connectors. As above, I didn't even
power this one up, so I don't know what the symptoms were. This
fix required replacing four 330uf/35VDC caps. I didn't have that
many such caps in my parts box, but a quick trip to Vetco (on Sunday!)
took care of that. While I had the unit open, I wiped the two
major heatsinks free of thermal compound, then replaced the compound
with new from a tube I keep in my parts bin. I also reheated a
couple of suspicious looking solder joints on the power board.
The repaired monitor has excellent color and brightness, and will make
a nice addition to my computer room.
Dell 1908FPt (added 16 Jan 2014)
I picked this one up from a local company that had it destined
for the recycle bin. When I powered it up, I heard a sizzling
sound from the lower corner of the case and smelled a lot of
ozone. I removed power, opened up the case and noticed a large,
discolored area on the metal case, near the lower set of high-voltage
wires that connect between the PCB and the CFLs that light the
display. I carefully connected the 120 VAC and switched on the
monitor, being VERY CAREFUL to keep both hands away from the
high-voltage leads. I could see an arc between the wires and the
frame, and the insulation had been melted on both the blue and pink
wires on this harness.
I powered down and removed the AC cord, then cleaned up the brown crud
that had piled up around the wires. I laid down a piece of
high-voltage insulation on the frame beneath where the wires run.
I also wrapped at least ten layers of electricians tape around the blue
wire and around the pink wire, to provide additional insulation.
I then reconnected the 120 VAC and switched the monitor back on; no
sizzling sound and no ozone. However, the brighness on the lower
half of the screen is noticeably dimmer, though the monitor is
certainly still usable. So far, so good; looks like one of my
easier and cheaper fixes.
BTW, after I reassembled the monitor, I tried to adjust the brightness,
but hitting the Menu button brought up a big padlock image on the
display and no access to OSD features. A quick check of the web
shows that for this monitor and several other Dell models, you just
keep the Menu button pressed for about 15 seconds and the locked icon
switches to an unlocked icon. Press the Menu button again, then
one more time, and you should have full access to the OSD features.
Dell P1913Sf (added 30 Aug 2014)
A guy from a local company told me this monitor just didn't light up
and asked me if I wanted to try fixing it. Sure! When I
shook the monitor, I could hear small bits of something rattling around
inside; that's never a good sign. Upon opening the case, I found
small bits of glass that looked similar to CFL tubes, which is an even
worse sign. But the screen and CFLs are enclosed in a single,
sealed unit, with no way for any pieces of glass to escape. I
figured the glass pieces were from something else, and not related to
the monitor not working.
I opened up the power supply case and was immediately impressed with
the quality of the design. The power board layout is spacious,
all the caps looked perfect, and the high-voltage circuit had been
reduced to a single, small PCB (about 1" x 1.5") with a very narrow
ribbon cable for connecting to the screen module. However, this
ribbon cable was NOT connected to the screen module, it was flopping
around loose. I must have dislodged it when I opened up the unit.
Since I couldn't find anything obviously wrong on the power board, I
reassembled the chassis, plugged the ribbon cable back into the
connector on the screen module (this is a TINY slot near the bottom
edge of the screen module), plugged in the unit, and turned it
on. It lit right up and worked perfectly.
My theory is that the HV ribbon cable is the culprit here. The
connector surface where the ribbon plugs into the screen module is very
thin and very tiny, and is not gold plated. I suspect that after
only two years of use, enough corrosion built up between the ribbon and
one of the connector pins in the screen module that the screen's CFLs
did not get the ON signal they need, so they didn't light. When I
pulled the ribbon loose, then reconnected it, I wiped free the
corrosion. If this theory is correct, I imagine more of these
monitors will begin appearing as defective or non-working. If so,
grab them; this was probably the easiset fix I've had to do.
This is a great monitor, with USB, DVI, VGA, and Display Port support.
Home